Although ISUT refers to Upgrading it’s an Enhanced Oil Recovery method that uses upgrading as its commanding chemistry. Being a very disruptive EOR process for the heavy oil reserves, ISUT requires explanation to avoid both misunderstandings and myths. Essentially, ISUT brings secure and safe nano-technology and an smart process configuration to make economically successful producing medium quality oil from reservoirs containing6 to 15 °API oils in situ, either mobile oil like in. most parts of the populated world or immobile oil like in closer to the poles areas of which the Canadian Oil Sands are an example.
The oil ISUT produces to go to the market from the moment it is applied, is higher than 19 °API, 100% transportable (no diluent), low sulfur, and ready to market. ISUT uses extremely small amount of nano-catalyst injected only once and for all during a short period of time (few months) and after that it continuously injects a Dense Hot Fluid (DHF) obtained from the same heavy oil being produced, to perform Enhanced Oil Recovery.
ISUT is the most advanced integrated, experimentally and numerically simulated Thermal Enhanced Heavy Oils Recovery process coupled with In Situ Upgrading reactions. The owner of this process, Nanostech Solutions, partners with oil producers to provide adequate configurations and techno-economic Engineering for a preliminary assessment on how the technology will maximize economics, exploitation efficiency and would allow close to zero emissions during the activity.
After securing a minimal injectivity created for the well to be used as injector, and after pre-heating the injector well at T higher than 180oC (with recycled diesel, for example) the DHF initially containing catalyst nanoparticles at a very low concentration in the fluid (less than 800 ppm) is to be injected. From this initial moment an oil 19oAPI and the field is ready for the Enhanced Oil Recovery from ISUT.
But how is that 19oAPI oil, fully transportable without need of any diluent can be produced?
ISUT essentially consists in recirculating back to the reservoir a fraction of initially produced extra heavy oil to carry heat and nano-catalysts to the reservoir using one-of-a-kind unit. While the heat injected with that DHF reduces effectively the viscosity in the surroundings of the injector well, the nano-catalysts attach firmly and irreversibly to the rock of these surroundings. The temperature in the injection zone is therefore increased to upgrading levels (above 280oC but always below 360oC) becoming that limited rock zone a catalytic reactor. The continuously injected hot residual oil (making the DHF) is permanently submitted to well-controlled upgrading reactions with hydrogen minimally and homogeneously dispersed in the DHF (at less than 1.2% in mass). The nano-catalyst used by ISUT is injected during a short period of time of three to four months, while the residual oil mixed with hydrogen (or the heaviest fraction of it, if preferred) is continuously injected into the reservoir and upgraded in the small portion of rock surrounding the injector well, where the nano-catalyst has been firmly anchored.
Not using hydrogen would imply deterioration of the quality of the produced oil, which will contain numerous light olefins, diolefins and aromatics. Lack of hydrogen will cause propensity to hardly breakable emulsions formed with connate water produced and serious risks of reservoir impairment, this is what other supposedly in situ upgrading processes such as In Situ Combustion or non-hydrogen injecting “catalytic in situ upgrading” don't disclose.
A cyclic application mode could as well be configured with an eventual separation unit, resulting in the injection of a residual oil fraction to carry heat, catalysts and to be converted into light diluents to EOR from the reservoir. Additional taking capabilities are needed during this intermittent mode, which is less efficient that continuous multi-well ISUT. The injection of full range oil may also be used when field facilities limitations impose it and/or when demo tests want to be produced at minimum cost. The EOR benefits are fully captured injecting full range oil, however the upgrading level is reduced when using whole oil, depending on the oil and hydrogen availability.
When sufficient development of an extra heavy oil field has been made, and sufficient wells are already developed, or also, when a green field development using ISUT is planned, the continuous version of the technology can be implemented with more efficient results by incorporating up-scaling design. For instance, one injector well surrounded by several producers could reduce significantly the number of catalytic injector wells, and result in a more efficient and faster oil recovery.
In figure 1 ISUT is presented in a continuous operation mode and with residual oil injection, the residue could be atmospheric or vacuum residue. The Advantage of injecting residual is that from the first moment very good quality oil, fully stable is being produced at the surface, increasing quickly with time, increasing the quality and rate of oil production even before full technology deployment. An specialized analysis of the technology for the specific purposes and characteristics of the client’s reservoir can be performed by this office to guide the interested producers through the span of options to consider.
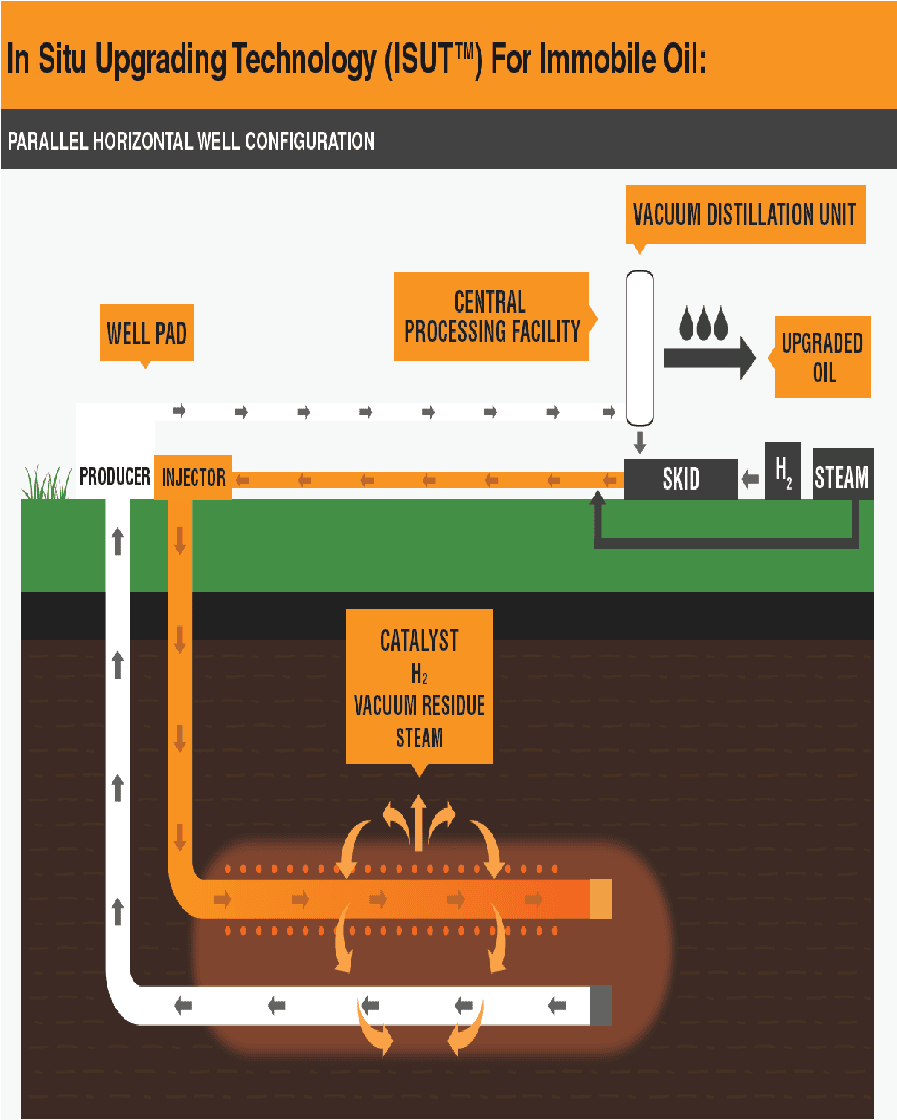
Figure 1. The incoming oil carrying heat to the reservoir starts upgrading right from the skid and all the way down to the reservoir, this is also what happens in the huff and puff mode. The upgrading process produces gases and light hydrocarbons, i.e. diluents or solvents that further reduce the oil viscosity and detach the oil from the reservoir rock. The fact that continuous injection is maintained (therefore continuous production at the surface of light oil is sustained) a permanent expansion of lighter materials in the reservoir occurs, creating additionally a push mechanism to enhance recovery.
It is convenient to emphasize that this method starts producing light oil from the moment the residue is injected.
The nano-catalyst is injected along with these fluids only during an initial period of 3-4 months. During this short period catalyst nano-particles brought to the surrounding of the wellbore carried by the DHF, will stick to the rock in the reservoir. Given the high temperature (350oC>T>280oC) the adherence of the nanoparticles is 100% ensured. Once sufficient catalyst has been placed in the reservoir iat the surroundings of the injection well, only oil and hydrogen blended keep being continuously injected. Its to emphasize, that the nano-catalyst being extremely reactive particles at the temperature of the process strongly adheres upon contact with the rock surrounding the injector well, it never flows to the surface, it doesn’t move out from the hot zone, exactly like in a catalytic reactor in a chemical process. In fact, what is performed during this brief period is the construction of a catalytic bed reactor all around the injector well. Through that catalyst cylinder the injected DHF will be continuously passing thus converted into diluent/solvent hydrocarbons. That cylinder in figure 1 is represented by the orange dots above and below that well.
For carbonate rock reservoirs, years of R&D have shown that the light gases, produced from upgrading in the reservoir plus the heat propagated, penetrate the microporous structures within the reservoir rock (i.e. carbonates) and through a combination of mechanisms(dilution, viscosity reduction, push) extract the oil present in the porous matrix of carbonate rocks, typically occurring in heavy oils reservoirs in Mexico (about 1 km deep) and in Canada’s Northern Alberta.
The EOR mechanisms that ISUT integrates are:
- Increased heavy oil mobility: by continuous heat injection, which reduces oil viscosity in the confines of the injection well.
- Push mechanism: by permanently injecting hot oil, which upgrades with a positive delta of about 8 API within the reservoir.
- Heavy oil dissolution by the light gases and distillates produced via upgrading.
- Extraction of heavy oil trapped within micropores of carbonate reservoirs, by gas penetration and light fractions dissolution with the oil in the matrix.
- Heat expansion of the rock in the surrounding of the injection well, which further opens the matrix pores to enhance internal fluids extraction, especially in carbonates.
- UPGRADING of the oil or the residual fraction being continuously injected. This upgrading is significant, a delta in API of more than 8 API occurring, even further if wished by increasing the amount of catalyst and whenever possible the injection temperature and pressure. However, the oil produced in the continuous mode(when a distillates separation unit is present) allows producing light oil only and the residue is permanently circulated back to the reservoir and upgraded!!
This is the breakthrough technology that allows thermal enhanced oil recovery of very heavy oils and pipelining only light oil-residue-less. An illustration of how the technology can be configured in pads is presented in the next figure 2.
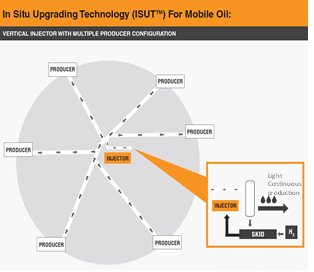
A number of producing wells can be placed and connected to a central facility where the unit will operate to inject the DHF stably. This DHF will initially also carry the nano-catalyst, this until the reservoir rock surrounding the injector becomes an upgrading reactor, meanwhile heating up that reaction zone. Once the catalyst has been sufficiently Incorporated, the facility will work only as DHF injector, making the operation extremely simple.
The Cat-SkidTM is designed to be online monitored, or by field operator contractors or by oil producing personnel in a very simple manner.