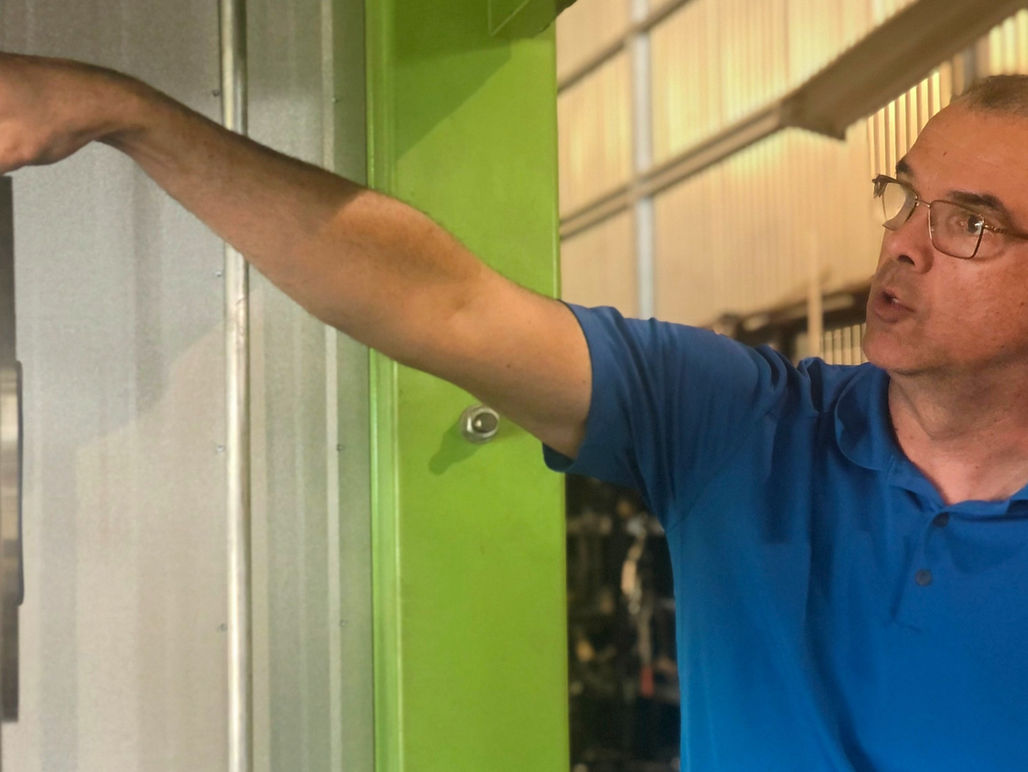
A new study concludes that Canadian oilsands producers have steadily improved their environmental performance from a greenhouse gas emissions (GHG) reduction standpoint - but a technology developed at the University of Calgary (U of C) could virtually eliminate those emissions.
The study, by IHS Markit, is entitled The GHG Intensity of Canadian Oil Sands: A New Analysis, reaches the conclusion that the combined GHG intensity of Canadian oilsands projects fell by 20 per cent between 2009 and 2018, the most recent year in which they were tracked.
The study, headed by Calgary-based analyst Kevin Birn, vice-president, North American crude oil market for IHS, also concludes that if the trends from 2009-2018 continue the GHG intensity of oilsands plants will decline by at least 16 to 23 per cent by 2030. That would mean the overall GHG intensity of the oilsands would be 30 per cent below what they were in 2009 by 2030.
“Based on the trend we’re seeing there seems to be a continuous effort to drive GHG intensity down,” Birn told oil and gas industry information source Daily Oil Bulletin.
“It looks like they (oilsands operators) are driving a long-term trend.”
One of the keys to producers having lowered the GHG intensity of their plants, both in mining and SAGD operations, is by productivity and efficiency improvements in their plants, Birn said.
He said new technologies play an important role, while factors such as the nature of the reservoir and the creativity of producers also play a role.
But what if there was a technology available to producers that not only reduces GHG emissions dramatically but does it in a cost-effective way and unlocking pipelines and markets for the oilsands?
Well, it turns out that there is - and it has been developed right on the doorstep of those oilsands plants, at the University of Calgary. (U of C)
Prof. Pedro Pereira-Almao is convinced the in-situ bitumen and heavy oil upgrading technology he and his team at the U of C have developed can reduce carbon dioxide (CO2) emissions by 80 per cent by eliminating or drastically reducing the use of steam and production costs, unlock pipeline limitations, by elimination diluent and opening markets with a higher quality oil.
Given that, it’s likely just a matter of time before the technology, developed at the facilities created by the Alberta Ingenuity Centre for In Situ Energy, will be widely adopted.
Pereira-Almao was a senior heavy oil researcher in Venezuela for 14 years and has since spent over 16 years at the U of C.
The technology he and others at the U of C developed utilizes a nano-technology
catalyst approach, whereby nanoparticles attach themselves to rock around an injection well, extracting an oil that bubbles to the surface as a light crude, with an API of 22 to 25, far beyond the eight to nine API crude that is produced now using SAGD.
Furthermore, he and his colleague researchers developed a field steam upgrading technology, also using a catalyst, which activates steam and CO2 to produce a lighter crude on field.
“I think we’ve come up with the right solutions at the right time,” said the chemical engineer, who is with the department of chemical and petroleum engineering at the U of C.
“Our huff and puff approach eliminates the need for diluent. It converts bitumen in the field to a crude with an API of 22 to 25 and the recovery from the reservoir is amazing, compared to SAGD.”
It can be applied to the shallower, thin deposite, as well as to those currently being exploited.
He and others at the university now want to see the technology widely adopted. To fast-track that adoption he and some fellow researchers have formed Nanos Tech, which he heads as the CEO. The thinking is that a company with an entrepreneurial bent - and other catalyst technology approaches - will be able to turn Calgary into a technological hub for catalyst and nanoparticle technologies.
NanosTech is now working to commercialize its ISU technology (ISUT), which can be easily adopted without radically altering existing SAGD facilities.
It only required a skid, which is used to introduce the catalysts into the reservoir. His research lab can produce maquettes to simulate any configuration and conditions requested, any environment desired, and both the experiement’s numerical simulation and the corresponding reservoir simulation that matches the field under construction.
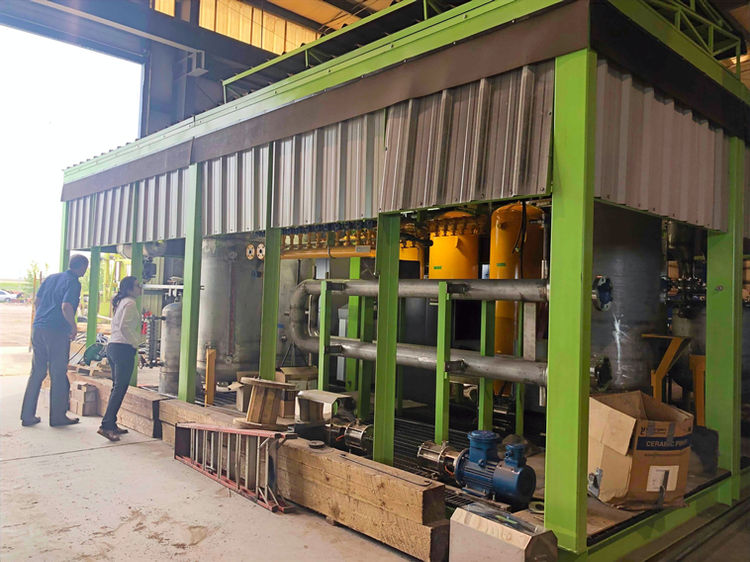
The ISUT possess begins with hot bitumen emerging from the production well, which in one configuration is then sent to a distillation tower or reheated to reaction conditions and mixed with the nano catalyst and hydrogen to be returned to the well.
During the first three to four months or so of the ISUT application, the skid would add nano-catalysts to the heavy oil. The nano-catalysts stick to the rock around the injection well, essentially turning the reservoir into a chemical reactor, similar to what is found in a refinery.
ISUT would increase the high temperatures to upgrade the bitumen to light oil, without the generation of petroleum coke.
Using the nano-catalysts, undesirable metals and vacuum residue are absorbed within the reservoir.
Pereira-Almao likens the process to “slow-cooking”.
The technology has been developed as a result of funding from the Alberta Ingenuity Centre and other Alberta government funding, as well as funding from five oilsands producers and many other companies not operating in Canada.
Pereira-Almao is hoping the creation of Nanos will play a key role in helping to make the oilsands more sustainable, especially since the technology has been improved since the oil and gas sector entered its current downturn in about 2015.
“In 2015 everything started to decline, but the crisis opened up opportunities,” he said. “For instance, we’ve doubled the cooking (processing) size since then.”
Meanwhile, it has been able to ramp up the ISU technology, thanks to signing a $30 million
contract in 2013 with the Secretary of Energy of Mexico, which would see the technology used by state-owned Petroleos Mexicanos (Pemex). The Mexican Institute of Petroleum secured $22 million for all the facilities to be created in field. U of C received $3 million and $5 million for the fabrication of the nano-cat skid unit.
The contract funding allowed the U of C researchers to have Calgary-based oil and gas equipment manufacturer Braeside Fabricators Inc. build a nano-catalytic skid that is at the core of the ISU technology.
The good news is the skid has been built and Nanos Tech can duplicate it and develop another skid for deployment in Alberta in a few months.
“The application in site developed facilities like the oilsands, costs very little,” he said.
A commercial version of the skid can be used to produce up to 5,000-10,000 bpd from each well.
“We would use the same approach in Alberta,” said Pereira-Almao.
A new skid, which would cost about $5.7 million to build, could be manufactured in months and deployed quickly.
Alternatively, if the existing skid isn’t deployed by next year in Mexico - which Pemex has said will happen - Nanos might be able to utilize it in a pilot project format meanwhile.
“We have the skid,” he said. “We can demonstrate the technology very quickly in Alberta.”
The skid, a NanosTech patented unit which consists of two decks, 12 metres long and six metres wide, can be moved by truck.
“It’s a no-brainer,” he said. “Alberta heavy oil and bitumen producers could compete (economically) with Saudi Arabia.”
He said Nanos Tech understands the struggles our industry is facing and would offer its patented technology to an eventual user essentially “for free”.
“The only thing they would buy from us is the skid,” he said.
Contact us for more information.